Hollow Fibers: ARPA-E Funding Supports Development Of Membranes And Sorbents For Carbon Dioxide Removal From Flue Gases
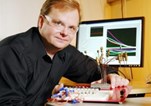
Researchers at the Georgia Institute of Technology are using funding from the Advanced Research Projects Agency – Energy – also known as ARPA-E – to pursue two different, but related, approaches for removing carbon dioxide from the flue gases of coal-burning power plants.
Power plants produce approximately one-third of all carbon dioxide emitted in the United States each year. The researchers will attempt to use the unique high-density properties of hollow fibers to develop cost-effective techniques for removing large volumes of the greenhouse gas from the emissions.
In one project, awarded directly to Georgia Tech, researchers are developing hollow-fiber composite membranes that will use nanoporous metal-organic framework materials to separate carbon dioxide from the flue gases. In the other project, Georgia Tech researchers are assisting colleagues at Oak Ridge National Laboratory in developing hollow-fiber sorbents that will soak up carbon dioxide like a sponge – then release it when heated.
Both will take advantage of the very high surface-to-volume properties of hollow fibers spun from polymers. For the membrane project, researchers envision providing a million square meters of membrane area within a moderately-sized building using the compact footprint allowed by the fibers.
"The challenge with this is to have a technology that not only physically works, but that can be built on a large scale and operated inexpensively," said David Sholl, who leads the membrane project as a professor in the Georgia Tech School of Chemical and Biomolecular Engineering. "If we are successful, this technology could have a very significant impact on trying to reduce carbon emissions from the combustion of coal."
Capturing carbon dioxide emissions at power plants makes sense because the emissions are concentrated there, Sholl says. But current technology, which involves bubbling stack gases through an aqueous solution and then removing the carbon dioxide, would consume at least a third of the energy produced by each power plant.
Membranes could theoretically separate the carbon dioxide from other gases with less energy input. But no existing membrane materials can do the job while being robust enough to operate in the hostile flue-gas environment – and inexpensive enough for the large areas needed.
"The volume is truly incredible any way you look at it – how much coal is burned or how much gas is produced per second," said Sholl, who is a Georgia Research Alliance eminent scholar in energy sustainability. "With a really good membrane, we would need something like a million square meters of area per power plant. That amount sounds impossible, but it's something already being done in water desalination facilities."
Hollow fibers no thicker than a hair are the key to providing sufficient membrane surface area, said William Koros, who is working on both projects as a professor in the School of Chemical and Biomolecular Engineering.
"Depending on the details of the design, the contact area that can be packaged into a cubic meter of membrane or sorbent volume can be hundreds or thousands of times higher than could be achieved through competitive approaches," said Koros, who is a Georgia Research Alliance eminent scholar in membrane science and technology. "This would allow us to fit the new carbon capture materials into already-cramped power plants."
Sholl and his colleagues are using computational techniques to screen the nearly 5,000 compounds that could be used in the metal-organic framework materials, which are sub-micron-scale crystals that will be added to the fibers to separate the carbon dioxide from other gases. Using the computational techniques, they hope to cut the number of candidate materials to as few as 50 that would be synthesized and tested.
"We are trying to connect the computational screening and prediction to a material that can actually be used in a membrane," said Carson Meredith, also a professor in the School of Chemical and Biomolecular Engineering. "We will study these compounds in a rapid way, measuring just the key properties of interest."
Those properties include permeance – the ability to allow carbon dioxide through – and selectivity, which will allow it to exclude other gases. That screening should cut the number of candidates to a handful that would actually be used to make membranes for more detailed testing, Sholl said.
At the end of the two-year grant period, the researchers expect to have produced and tested hollow-fiber membranes at the laboratory scale. They would then partner with a manufacturer to produce bundles of the fibers for a pilot-scale test.
Power plant flue gases contain nitrogen oxide and sulfur oxides, as well as moisture, which can combine to cause corrosion. Moisture alone can also cause problems for some membranes. In addition, flue gases contain trace amounts of compounds such as chlorine and mercury that could also harm the membranes.
"We won't really know what the contaminants will do until we put the membrane into the flue-gas stream," Sholl said. "A key issue will be to show that these materials will work today and tomorrow, and for a long time afterward. The robustness of the materials in a real environment is something that we have to understand."
A carbon capture system based on the hollow-fiber membranes could potentially remove as much as 90 percent of the carbon dioxide from plant emissions. But that would come at a cost: even in the best-case calculations, removal would require at least 10 percent of the plant's energy.
"The reality is that all countries around the world are going to burn coal for the foreseeable future," Sholl added. "We really don't have a choice because we don't have other good sources of baseline load at the level we get from coal. Any technology to economically capture carbon from these facilities could have a big impact."
In addition to those already mentioned, the membrane project includes Krista Walton, Christopher Jones and Sankar Nair, all professors in the School of Chemical and Biomolecular Engineering. The projects are funded through the American Recovery and Reinvestment Act of 2009 (ARRA).
SOURCE: Georgia Institute of Technology