Transformer Oil Coolers: Essential For Ensuring Optimal Operations
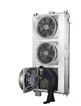
Transformer oil coolers play a critical role in keeping electrical generation systems reliable. Transformer oil coolers are a small investment that protect the power industry's huge capital investment in the massive transformers that make up the backbone of a nation's energy supply.
Power plant generators produce electricity that has to be converted to high voltage for more efficient transportation across wires to substations near businesses, factories and homes. The transformers that convert the electricity to high voltage do so extremely efficiently with only something in the order of 0.5% of the electrical load being lost in the form of heat. Even though the loss percentage is small, the actual quantity of heat can be quite large. The heat that is produced must be carried away from the transformer and dissipated. If not, the transformer will overheat and be damaged or even destroyed.
The windings of the transformer are immersed in an enhanced mineral oil that is circulated to cool the transformer. This oil also remains stable at high temperatures and has excellent insulating properties that protect against stray current path. The oil circulates through both the transformer windings and the cooler and the heat lost is transferred either to the ambient air around the transformer or to water. The oil-filled tank often has radiators through which the oil circulates by natural convection. Large transformers use forced oil circulation by electric pumps, aided by external fans or water-cooled heat exchangers.
The transformer oil cooler has to be sized to transfer the amount of heat that needs to be dissipated from the transformer, depending on its size, design, and configuration. Some transformer oil coolers are designed to take into effect the kinds of adverse conditions around the transformer that could potentially cause a shortfall in performance.
Design Considerations to Ensure Performance
Air-cooled systems most prevalent
Most fossil fuel plants use air-cooled systems because air is always readily available and its use in transformer oil cooling systems usually involves fewer environmental concerns.
There are several design considerations that must be taken into account with air-cooled systems. The temperature difference between the oil and the air determines the amount of surface needed for cooling. The greater the temperature difference between the oil and air, the less surface is needed. So if the air temperature has been elevated but the oil temperature is fixed because the application cannot allow it to increase, the size of the cooler's surface area must be increased as a result.
Air-cooled transformer coolers are typically mounted on the side of the transformer, usually vertically about 3 feet or 1 meter away from the transformer wall. The coolers take air from around the transformer, and fans then draw or push the air through the transformer coolers. The air is then discharged to the environment around it. To get the level of cooling required, designers must be able to accurately predict the amount of air that will actually flow across the heat exchanger as well as the temperature of that air.
Depending upon how many coolers are required and how much heat has to be dissipated, one to six coolers might be placed along each side of the transformer. The more coolers mounted along the side of the transformer, the more likely there will be adverse air recirculation from the discharge of that air. This is because the discharged air is warmer than before, and if blended with the air that is being drawn in to cool the transformer, the discharged air will raise the temperature of the air that's coming through.
Several other site-specific factors must be taken into account to avoid detrimental affects on cooler performance:
- Wind speed and direction can be a factor - for example if fans are blowing air away from the transformer but the prevailing wind is blowing towards the transformer, warm air will be pushed back.
- Buildings around the transformer, firewalls or other fire protection components can trap air and impede air exhaust.
- Existing transformer cooler applications elsewhere on the site could blow heated air toward the new installation.
For example, a designer may be asked to design a system based on a 30 Celsius (°C) ambient situation. However, due to one or more of the factors described above, the air immediately adjacent to the transformer might not be 30 °C, but could possibly be as high as 35 °C to 50 °C. Experienced designers know to design a system that reflects these actual ambient conditions.
Water-cooled systems
Water-cooled transformer oil coolers are considered more efficient, and are used where water is plentiful, for example in hydro power applications. After the heat from the transformer is dissipated to the water, it is necessary to either discharge the water back to its source (which has potential environmental issues), or lower the water temperature before recirculating it through the transformer cooler (which requires an auxiliary system). Also, water-cooled systems require a leak detector system to make sure water doesn't get into transformer oil and then into the transformer, which could have disastrous consequences.
Unifin International, LP manufactures transformer oil coolers that are fitting for numerous different applications in the power generation and power transformer industry from nuclear to hydro electric to gas-turbine power. They are made for the most efficient heat transfer in the most demanding settings with long-lasting durability and low cost in mind.
Fans and Motors are Key
Another factor that makes a big difference in the operation of the transformer oil cooler is the selection of the fans and motors for the unit. Designers must size the motor correctly to drive the air without overheating the motor. Motor cost, cost for required circuitry and/or need to use existing circuitry, and noise levels are factors that must be considered.
Experience shows that if fans and motors are selected based solely on the manufacturer's specifications, they may not perform as required. Fan and motor performance specifications are usually based on optimum conditions, inconsistent with the extreme environment of most power applications. In these conditions, fans frequently require more energy than specified, requiring larger motors which in turn use more power.
To deal with this issue, Unifin International, LP developed a set of specifications for transformer oil cooler fans and motors that meet the power industry's need for reliability, efficient power consumption, and the ability to withstand the various ranges of temperature and other weather conditions encountered. Unifin selected a series of efficient, low-noise fans, conducted specialized tests at the revolutions per minute (RPM) that might be used with various cooling applications, and measured air flow versus pressure loss and power consumption of the motor and noise of the fan. Based on the results, Unifin developed its own set of fan curves of air flow versus pressure loss for each of the fans at each RPM they would be using, and selected motors that would meet the specifications.
Manufacturing Process Must be Strictly Controlled
Manufacturing processes must be strictly controlled to ensure that the oil cooler meets the specifications. For example, Unifin's transformer oil coolers use integral finned tubing formed using an extrusion process that hardens the aluminum so the fins are very strong, resulting in optimal heat transfer efficiency and exceptional durability. Unifin also offers a high quality plate-fin technology as a premier heat transfer surface in a more compact design. The plate-fin surface can be augmented to enhance performance. As a result the specified heat to be dissipated can be done with less material.
Maintaining cleanliness of the internal surfaces of the cooler during manufacturing is extremely important, especially surfaces that would come in contact with the circulating oil. It is essential that no metal particles are introduced that could contaminate the oil. Particles that could get into the transformer windings with the oil would be extremely detrimental to the life of the transformer.
In addition to a clean manufacturing process, cleaning processes like a flushing system and electronic monitoring or particle counting systems can be insurance that the system will perform as required and protect the transformer.
Oil Coolers Protect Transformer Investment
Power facilities must perform continuously, often in extreme environments. Properly sized and configured, high quality transformer oil coolers play a vital role in maintaining safe, efficient, and reliable electricity production. Overheating can shorten the transformer's life, and in severe cases, could lead to serious and costly damage or even destruction of a transformer. Cooling the transformer is affected by the varied conditions that can occur, and special care is needed to design cooling systems that actually reflect the existing ambient conditions on the site.
For more information on air- or water-cooled transformer oil coolers, please visit www.unifin.com.
SOURCE: Unifin International, LP