American Superconductor targets the grid
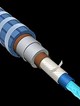
By Joe Palenik
While some are targeting low generating reserves and others are looking at cutting demand as ways to ease the strain on power grids, American Superconductor (AMSC) of Westborough, MA, is targeting the grids.
The company is banking that its high-temperature superconductor (HTS) systems will be accepted as an industry standard, according to Greg Yurek, CEO, who said that the company is revolutionizing the way the world uses electricity. "That's quite a mouthful, but in fact we're doing it," he said. (See sidebar, "Getting down to the wire with Greg Yurek, AMSC".)
For those not into cryogenics, "high-temperature" appears to be a misnomer. American's system operates at 77 degrees on the Kelvin scale, where zero degrees indicates the total absence of heat. On the Centigrade scale, 77 Kelvin translates into minus 196. That's still mighty cold, but it's high temperature in the world of cryogenics.
Superconductivity interest rekindled in mid-80s
Superconductivity at low temperatures became more than a laboratory curiosity about 15 years ago, when scientists discovered some materials that posed little resistance to electric current as the temperature neared absolute zero.
Superconductivity at low temperatures isn't a new thing. As a laboratory phenomenon, it was discovered around 1911 by a Dutch physicist, and it remained virtually ignored until the mid-80s, when the new family of compounds was discovered that exhibited extremely low resistance to current at low temperatures.
However, the materials were ceramics, normally insulators and not the easiest thing to turn into wire, which must have some flexibility. Yurek, previously a metallurgist, came up with a way to draw the brittle material into filaments, much like fiber-optic cable, and earned a patent.
Superconductors have to be kept cold to operate, and the company says the efficiency is well worth the cost because the cold cable can carry about 100 times more capacity than conventional cable the same size.
Operating at 77 Kelvin instead of closer to absolute zero saves considerably on cooling cost, which the company says makes the product much more attractive, efficient and easier to install and maintain. American Superconductor manufactures the wire and ships it to Pirelli Cables & Systems, which turns it into cable, which is pictured to the right.
Detroit Edison to install cable
Detroit Edison plans to install three, 400-foot cables about four inches in diameter in its Frisbie Station beginning next spring. Those cables will contain more than 18 miles of American Superconductor's wire.
Besides the wire, the company has several products, including storage devices that can instantaneously release large amounts of stored electricity into a grid when there is a power drop.
One, known as SMES (Superconducting Magnetic Energy Storage), is available for hookup on the load side of, for example, a large industrial customer's meter. The unit instantly injects reactive and real power into any or all phases to dampen out disturbances and eliminate any havoc a voltage drop could cause to delicate computers or computer-controlled process equipment. According to American Superconductor, most outages are a second or so in duration.
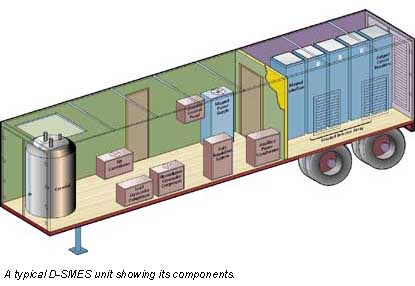
For larger applications, the company offers D-SMES. For distributed units, a company could interconnect to its grid to cull short-term voltage drops. The units recharge in around a minute and are ready to go again, the company said. In addition, they are mobile, which adds versatility.
Protection for power supply
According to the company, several SMES units at Tinker Air Force Base in Oklahoma handled power fluctuations from about 40 lightning strikes in less than two hours in May 1999, when Oklahoma City was hit by devastating tornadoes.
The units were protecting power supply for a data warehouse that needs reliable 24/7 power. The company said the units worked so well that the warehouse's battery backup system wasn't required to maintain power.
American and GE Industrial Systems, a unit of General Electric, are marketing and selling D-SMES to domestic utilities as a co-branded product. Entergy became the first purchaser through that alliance and plans to install its unit in Texas early next year.
WPS purchases, installs six D-SMES
Wisconsin Public Service (WPS) purchased six D-SMES units to handle voltage fluctuations in an isolated part of its service territory involving about 200 MW that has shown summer voltage problems. The area is fed by a transmission system that will be upgraded, according to Pete Hamacher, a regional electric engineer for the company.
The area includes a mix of industrial, commercial and residential load and is growing quickly, he said. A transmission line is planned to feed more electricity to that area, but that can't be accomplished immediately.
"We saw this problem, and we realized that this transmission line was not going to be in service in time," he said. "We had to do something up there."
However, the anticipated high-load problem did not develop. "At this point," he said, "we haven't truly used the units to their full potential, but we have noticed that the units have been operating. I would say have to say that it's probably around a dozen times that they've operated for less serious events on the system. They're there as a safeguard, so to speak."
Mobility an asset
Hamacher said the mobility, which allows the unit to move to wherever the problems occur, remains a key asset. Once the need disappears, the units can be moved to other parts of the system, sold or used for industrial customers concerned about power quality.
He declined to discuss cost. However, American Superconductor lists the cost of a D-SMES at US$650,000 to US$800,000. And, according to Yurek, Wisconsin Public Service's agreement includes a buyback arrangement.
The installation of the units didn't require any exotic hardware, Hamacher said, adding that there were few installation glitches. The biggest installation problem was communicating with the units, which generally were installed in remote areas.
"We went to a cell-phone link," he said. "We had some problems getting the cell-phone system squared away. It took a couple of months."
Industrial motors show promise
Another promising market is industrial motors.
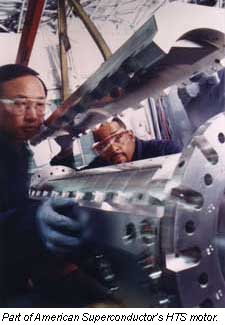
American and Rockwell Automation, part of Rockwell International, last July announced the world's first 1,000-horsepower HTS industrial motor, which Rockwell dubs as an important energy-saving technology that will pave the way for more research and development and future profits.
The two companies said that the current market for large industrial motors amounts to about US$1 billion yearly worldwide, adding that the market for electric generators over 30 MW, which use about the same technology as motors, is about double that.
About the author: Palenik, 53, grew up in the coalfields of western Pennsylvania, where the economy at one time was tied heavily to coal and steel. He's been writing more than 25 years, about 15 of which covered energy and energy-related issues. He's freelanced for a variety of print and electronic publications, including about 10 years with a group of McGraw-Hill energy and business publications. writer@dmv.com.
Getting down to the wire with Greg Yurek, AMSC
Q What are the advantages of your technology?
A I think it's quite clear. The advantage of our product, HTS wires, is the ability to carry more than 100 times the power than a copper cable of the same dimensions. The high-power density of these wires translates into systems economics. For example, this means that HTS underground cables can be more cost effective on a systems basis, including savings on system upgrades, excavation and so forth, as compared with copper cables, even including the cost to cool.
Q How did your product begin?
A These new materials were discovered by two IBM scientists in Switzerland in 1986. At the time, I was on the faculty at Massachusetts Institute of Technology. I'm a metallurgist by training. These exciting new materials turned out to be ceramics. Ceramics are inherently brittle. In the winter of 1987, after hearing about the discovery, I worked with some MIT colleagues to come up with a way to "bend the unbendable" and make flexible wires. And that invention was the genesis, or the basis, for forming American Superconductor Corp., which we formed in April of 1987.
Q What are the financial possibilities for the wire?
A We look at Wall Street analysts. They see today a US$15-billion addressable market, just for applications in the power infrastructure, meaning generators, power cables, transformers, industrial motors and so forth. According to the analysts, this goes up to about US$25 billion in about 10 years. We're focused today on the power infrastructure, bringing solutions to the power industry, but we believe the same core products will apply as well in the medical, transportation and industrial processing sectors as well. As we grow our company over the next five to 10 years, we see ourselves expanding into additional market opportunities.
Q What is your biggest problem?
A One key challenge we have in front of us today, and we've been at this for 13 years, is manufacturing scaleup. We just broke ground in August of 2000 on a new manufacturing plant to make HTS wires that will start production in mid-2002. It's the first commercial facility for HTS wire in the world. Today, in our current operation, we're producing about 500 kilometers of this wire per year. The new plant will have a capacity initially of 10,000 km per year.
Q What problems does the technology solve for the transmission and distribution segments of the power industry?
A One is the demand for a lot more power and the inability of copper cable to carry all of the power that's being demanded, particularly in congested urban locations where additional space simply isn't available. These new high-capacity cables help solve that problem.
The second problem is reliability of the power, where you get short drops in voltages in the power system that can knock out manufacturing operations using sensitive equipment, for example. We have another product, SMES (Superconducting Magnetic Energy Storage), that takes advantage of the ability of a coil of superconducting wire to store a large quantity of electricity. Through proprietary electronic devices, we're able to tap into that stored electricity and deliver it very quickly, instantaneously, to a power grid to stabilize it when these voltage drops occur.
We can put out, for example, three million watts of power over one second, less over two. Most of the voltage drops, 80% to 90% of the time, are much less than one second. There's plenty of stored electricity there to solve those problems. We're providing something that takes care of these drops in voltages. It's a great solution to have at hand.
Q What about the motor technology?
A We've demonstrated a 1,000-horsepower industrial-size motor. The motor operates more efficiently because we're using superconducting wires. Improving the efficiency of the motor results in lower costs of operation. The extremely high fields generated by HTS rotor coils will also make these motors dramatically smaller and lighter. As a result, we expect them to be lower-cost to build, and that means increased profitability for the manufacturers that adopt the technology. (Return to main story)