Oil-Free Rotary Screw Compressors Save the Day
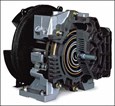
Steam turbines depend on compressed air as much as they do on fuel. Air actuates the valves, operator flow-down systems, controls the induced draft dampers and serves numerous other general utility purposes. Because air is also used for delicate instruments, it has to be oil-free. In this case, the consulting engineers determined a base load for each generator of about 1200 CFM (150 CFM maximum). They specified four, 600 CFM units to be staged for each generator.
For the first generator, the power company purchased four oil-free reciprocating compressors, which used Teflon rings to seal the cylinders. The price was about $100,000, and that's where the trouble began. Within one year, the utility had spent an additional $100,000 for repairs—almost enough to replace the compressors.
The Atlas Copco Solution
With repair bills threatening to overtake the original investment, it became clear something had to be done. The power company sent the plant engineer off in search of a solution. After visiting a pulp mill and a fossil fuel plant (both with Atlas Copco installations), the company had its answer—trade in reciprocating units for units with oil-free rotary screw compressors.
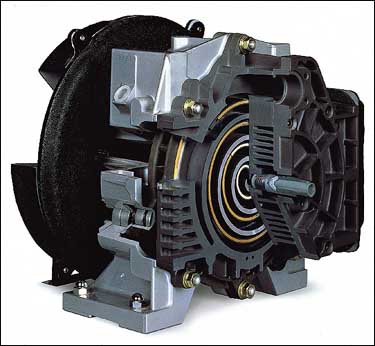
Cut away of oil-free rotary-screw compressor
When all bids were evaluated, Atlas Copco came in the winner. Several years later, when the second of the generators went on-line, the company bought four more Atlas Copco compressors. When the station is completed, there may be 16 Atlas Copco compressors working there, he said.
So far, the state power company has installed 24 Atlas Copco compressors around the state. These compressors are of various types and are used for various applications. The consulting engineer, who serves power companies in three states, sees it as a trend.
Trouble-Free Air
When compressors are in operation 24 hours a day, seven days a week, year-round, dependability is a key consideration. Of the eight units installed so far at the new plant, not one has ever been down. Repair bills are $0.
Oil-free reciprocating compressors use Teflon rings to seal cylinders. In the first year alone, repair costs on four 600 CFM compressors neared the cost of the original investment.
Atlas Copco's screw compressor delivered the same 600 CFM of oil-free air. To date, not a cent has been spent in repairs. When it comes to routine maintenance, Hersch said, there too the Atlas Copco units have proven advantageous. With fewer moving parts, rotary screw compressors seem to require much less maintenance than conventional designs.
Edited by April C. Murelio
editor@poweronline.com